views
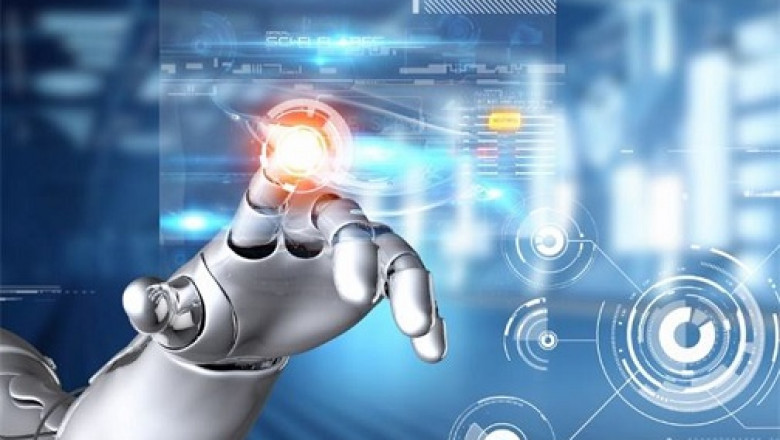
The positive electrode of the electrolytic capacitor is high-purity aluminum, the dielectric is the aluminum oxide film formed on the metal surface, and the negative electrode is a viscous electrolyte, which is equivalent to an electrolytic cell during operation. The common failure modes of aluminum electrolytic capacitors are: leakage, explosion, open circuit, breakdown, deterioration of electrical parameters, etc. The relevant failure mechanisms are analyzed as follows.
A. Leakage
The leakage of the working electrolyte of aluminum electrolytic capacitors is a serious problem. The working electrolyte is slightly acidic, and the leaked working electrolyte seriously pollutes and corrodes other components and printed circuit boards around the capacitor. At the same time, inside the electrolytic capacitor, due to leakage, the working electrolyte gradually dries up, and the ability to repair the anodic oxide film medium is lost, resulting in breakdown of the capacitor or deterioration of electrical parameters and failure.
There are many reasons for leakage, mainly due to poor sealing of aluminum electrolytic capacitors. When using the sealing structure in which the aluminum negative electrode foil is sandwiched between the shell side and the sealing plate, it is easy to leak electrolyte at the shell side. Capacitors sealed with rubber plugs may also leak due to rubber aging and cracking. In addition, products with problematic mechanical sealing processes are also prone to leakage. In short, leakage is closely related to sealing structure, sealing material and sealing process.
B. Explosion
The AC component of the aluminum electrolytic capacitor is too large in the working voltage, or the oxide film medium has many defects, or there are harmful anions such as chloride and sulfate, so that when the leakage current is large, the rate of gas generation by electrolysis is faster and larger. Part of the gas is used to repair the anodized film, and a small part of the oxygen is stored in the capacitor shell. The longer the working time, the greater the leakage current, the more gas in the shell, and the higher the temperature. The air pressure difference between inside and outside the metal shell of the capacitor will increase with the increase of working voltage and working time. If the product is not well sealed, it will cause liquid leakage; if the sealing is good and there is no explosion-proof measure, the air pressure will increase to a certain extent, which will cause the capacitor to explode. The leakage current of high-voltage large-capacity capacitors is larger, and the possibility of explosion is greater. At present, the explosion-proof shell structure has been widely adopted. A pleat is added to the upper part of the metal shell. When the air pressure is high, the pleat is opened to increase the inner volume of the shell, thereby reducing the air pressure and reducing the risk of explosion.
C. Open circuit
Open-circuit failure of aluminum electrolytic capacitors may occur when they work in high temperature or hot flash environments for a long time. The reason is that the anode lead-out foil is broken due to electrochemical corrosion. This failure mode is more common for high voltage bulk capacitors. In addition, after the anode lead-out foil and the anode foil are riveted, if they are not sufficiently flat, the poor contact will cause intermittent open circuit of the capacitor.
When the working electrolyte with DMF (dimethylamide) as the solvent is used in the aluminum electrolytic capacitor, the DMF solution is an oxidizing agent, and the oxidizing ability is stronger at high temperature. After working for a period of time, the capacitor may open circuit due to the formation of oxide film at the riveted part of the anode lead-out foil and the solder tab. Such failures can be reduced if an ultrasonic welder is used to hold the lead foils together with the solder joints.
D. Breakdown
The breakdown of aluminum electrolytic capacitors is caused by the rupture of the anodic aluminum oxide dielectric film, resulting in the direct contact of the electrolyte with the anode. Alumina films can be locally damaged due to various materials, processes or environmental conditions. Under the action of an external electric field, the oxygen ions provided by the working electrolyte can re-form an oxide film on the damaged part, so that the anodic oxide film can be filled and repaired. However, if there are impurity ions or other defects in the damaged part, so that the filling and repairing work cannot be completed, micropores will be left on the anodic oxide film, and may even become through holes, causing the aluminum electrolytic capacitor to break down.
In addition, with the increase of use and storage time, the solvent in the electrolyte is gradually consumed and volatilized, which increases the acid value of the solution and corrodes the oxide film during storage. At the same time, due to the aging and drying of the electrolyte, oxygen ions cannot be provided to repair the oxide film under the action of the electric field, thus losing the self-healing effect. Once the oxide film is damaged, the capacitor will break down. Process defects are also a major cause of breakdown in aluminum electrolytic capacitors. If the anodic oxide film formed during the energization process is not dense and firm enough, the oxide film will be seriously damaged in the subsequent cutting and riveting processes. This anodic oxide film is difficult to repair in the final aging process, so that the leakage current of the capacitor is very large during the use of the capacitor, and local self-healing cannot save the fate of the final breakdown. Another example is that when the riveting process is not good, the burr on the lead-out chaff will seriously injure the oxide film, the leakage current of the punctured part is large, and the local overheating will cause thermal breakdown of the capacitor.