views
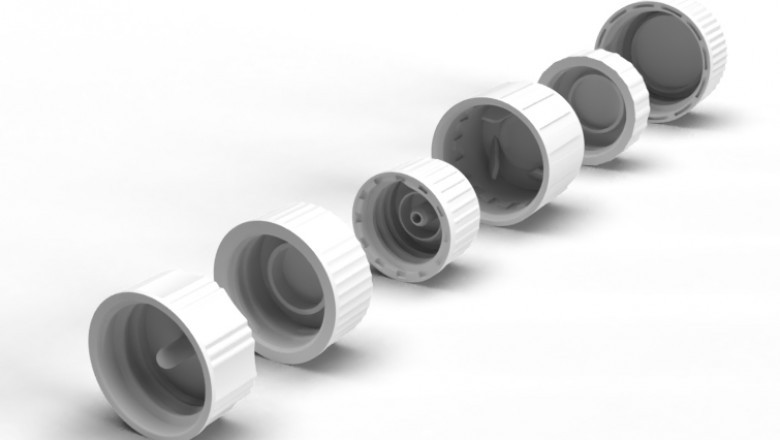
The Future Of Plastic Injection Molding
The processes of production and product design have developed as we've advanced from revolutionary breakthroughs like the light bulb to the telecommunications age of radio, phones, and TVs. The advancements in current injection frisbee are driven by computers, the internet, renewable electricity, and all that follows after. However, before we can grasp where we're headed, we must first understand how we got here.
What Is Moldmaking and How Does It Work?
Moulds must be created with extreme precision since they are one of the most significant manufacturing investments. To ensure that parts can be mass-produced with repeatable accuracy, modern plastic moulding manufacturers demands great precision.
This level of precision is also necessary for the design of the tools that are used to make, hold, or test objects during the manufacturing process. The following factors can influence the price of a plastic injection mould:
Metal Core
The material for a mould is heavily influenced by the projected time of a production process. Aluminium moulds, for example, are used for short production runs and short-term projects, while hardened steel (or a similarly robust metal) moulds are used for large production runs and long-term projects. When choosing a material for injection mould making, plastic injection mould manufacturer evaluate if it is more cost-effective to invest in a costly but long-lasting mould or to use a less expensive but less durable mould and replace it when it wears out.
Count of Cavitation
Most plastic moulding manufacturers, however, advocate using one mould per part instead, because they usually produce components of lower quality and performance.
When it comes to mould making, the number of cavities has an impact on the amount of time, labour, and money required. In general, fewer cavities in a mould design equals less resource investment, whereas more cavities equal more resource investment. Experienced chocolate packaging manufacturer should be able to optimise the number of cavities in order to achieve the highest production efficiency at the lowest cost.
The Mold's foundation
The cost of producing a mould foundation varies depending on the grade of steel used, modifications incorporated, and the size of the mould.
Machining of the core and cavity
All moulds are made to order to satisfy the application's component and production requirements. Cavities, cores, cooling lines, and ejectors are some of the mould parts that may be customised.
Part Difficulty
The more complicated the desired portion is, the more expensive the mould will be. Because the mould design must meet all of the component design criteria, including surface texture and tolerance, this positive link exists.
What Has Changed Since Then?
During the 18th and 19th centuries, plastic molds for chocolate making became popular. Toolmakers had to do practically everything by hand at the height of the Industrial Revolution. Creating tools, heat treating them, honing them, cutting metal, and drilling out the pattern by hand took a long time. Conformity issues developed often as a result of the uniqueness of everything manufactured by human hands, and no two moulds were exactly the same.
The following are two mold making technologies that had a key role in the shift from manual to computer-assisted machining:
Milling Machines with CNC Control
CNC milling machines began as two-dimensional Bridgeport milling machines with CNC accessories. For increasingly complicated moulds, today's milling machines enable even quicker speeds and precision.
CAD Software
By expediting the mould design process, CAD systems have had a substantial influence on the mould making industry's progress. They made it possible for industry experts to swiftly edit, test, and modify 2D—and eventually 3D—renderings. MIT's Sketchpad and the French UNISURF were among the first systems to transform the design process, and their more complex descendants are still used in mould making operations.
Moldmaking in the Future
Many industry executives have chimed in on what's occurring and what's ahead as manufacturing capabilities advance:
Plastic alternatives' chemical technology is not only advancing, but it's also swiftly becoming a requirement.