views
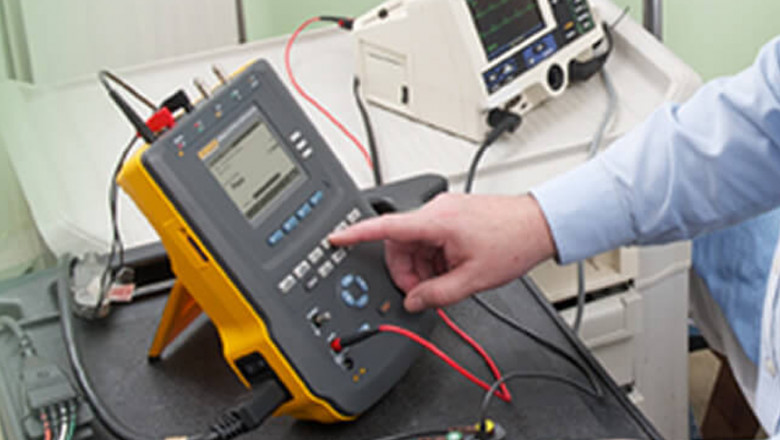
The emergence of such equipment has been a great relief for health care sectors, and it has resolved many cases very quickly. In short, we need it as a part of the current revolution in the medical industry.
Now, doctors feel very comfortable with the significant reduction of risk factors, reduction in illness, mortality rates. The technology is magical proof for radiographic, diagnostic imaging, diagnostic ultrasound, Fluoroscopic X-ray, dental procedures, and physiological monitoring of mammography.
If you as a medical professional do not have the acquired skills for using the equipment, it may serve some unintended consequences for you and your peers. It may create some issues with the patients as well. Hence, prior training including the reading of manuals is quite important.
You cannot miss the step of its handling, error reduction, and other techniques. Sometimes it malfunctions and it would trap others in great confusion.
Why do We Consider Biomedical Equipment Safety Inspection?
The Biomedical Equipment Safety Inspection proves to be healthful and helpful in many paths.
• It generates a prolonged life cycle for the equipment.
• It protects staff, patients, and assets.
• Regulatory requirements, approval agencies, and insurance companies stick to its testing & safety inspection before using it.
• Quality assurance is quickly marked.
• There is hardly skipping the concern of asset management.
Many renowned laboratories perform the inspection as per the requirement from the manufacturer’s end.
With measurable, orderly, and suitable methods, it is easy to assist in the projects and reduce events & accidents. Finally, further consistency is required for the equipment, and it takes great care in mitigating the risk factors.
The Process of Biomedical Equipment Safety Inspection:
All the Biomedical Equipment Safety Inspection Services are led by the lead inspector and analyst for pursuing the overall managerial tasks. Computer specialists, analysts, engineers also join the inspection process. The team would discuss and divide the duties for the concerned team members for the inspection.
The analysis is not generally inclusive, rather it is an audit. Thus, process, validation of data, test procedures, and controls are not reviewed at once. However, there are some specific coverages to mark the details of a few controls or systems. Application documentation and flow chart are worthy before proceeding with manufacturing steps and early inspection strategies.
The program of this Biomedical Equipment Safety Inspection Services considers adequate management, planning, and implementation. Planning would include physical, financial, and other personnel to back up the process.
After defining the program, other aspects are also taken care of and later managed for ensuring uninterrupted services. Proper implementation should not be hampered anymore until we collect accurate data for ensuring optimal functionality.
Services in Biomedical Equipment Inspection:
Some services have changed the medical and dental treatment processes. Following are the listed ones that you should remember:
• Physiotherapy and chiropractic rooms
• Consulting rooms for doctors
• CT rooms
• Dental surgeries
• Ultrasound rooms
• Treatment rooms
• Blood collection cells
• Nursing
• X-ray rooms
The whole inspection process is under strict compliance, and we must respect the process as per certain standards. After even completion of the job, there are many things like calibration of the equipment, taking the inventories, and then collecting accurate readings from this equipment.
The safety inspection would include:
1. Visual Inspection: It is very easy to go through and then check the manufacturers’ released specifications. It should not have any impurity or external damage. It would include a set of checks like contamination, housing enclosure, fuse rating, cabling, labelling and markings, the integrity of each part.
2. Earth Bond Testing: Here you will test for leakage currents, leakage in an enclosure, and patient leakage.
3. Earth Leakage Testing: It generally checks whether the medical equipment is under protective condition or not.
Each device has its identification data and documented proof about manufacturer model, location, serial number, and certain specifications. The data are required to process the task in an orderly manner and steps are to be followed without missing anything.
The major thing is to notice the pre-requisites we need for the equipment testing and then later decide its fate. The commitment to fulfil legal requirements and vitalities should never be compromised anymore.
If the product is found to be defective, quickly inform the manufacturer for immediate replacement. Sudden deficiencies may create serious trouble for everyone. Whenever we are advancing with such digital techniques, the responsibilities would arise more as far as patient protection, treatment, etc.
Typical illustration and major judgment are not everyone’s sense of visualisation. Hence, for its certain expertise and skills are to be adapted.
Get proper training in your healthcare centre if you do not have any idea about it. The better practice would inject necessary control and decision-making skills for you in the future. Have better testing before treatment!