views
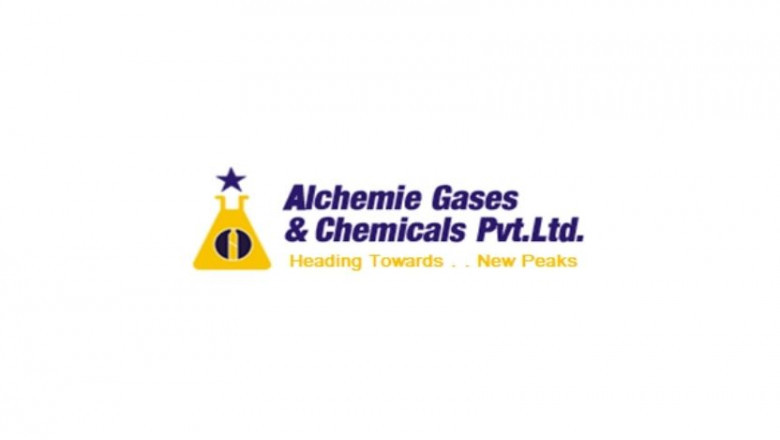
Have you ever wondered how some things receive their unique shapes and are manufactured? Industrial gases are often used in the manufacturing industry to establish the correct environment for various processes or to assist in the creation of the final product. The various processes used in the manufacturing industry to create consumer goods that use plastics, metals, and other raw materials are mentioned below:
Three-dimensional Printing:
3D printing, also known as "additive manufacturing," has revolutionized production in recent years by providing a cost-effective alternative to traditional methods. 3D printers build three-dimensional items by layering small pieces on top of one another to create a single final output. Industrial gases are necessary for successfully printing a 3D object since they aid in the creation of the proper atmosphere when printing in confined spaces. Argon and nitrogen are commonly used to create an inert or chemically inactive atmosphere in order to produce high-quality products. An inert atmosphere is essential for ensuring that the metal being produced is not polluted by the gases normally present in the air, as well as reducing the risk of combustion. This is critical when using a 3D printer to create high-quality items.
Injection Moulding:
Large plastics are molded into intricate shapes and designs using gas-assist injection molding, which is a part of the production process. Because nitrogen is an inert, dry, and non-toxic gas that melts at a high temperature while preventing oxidation, it is the best gas for the purpose. The heated plastic is injected into the mold during this step. Because the outermost section of the molten plastic melts first, nitrogen is swiftly fed into the mold, pressing the plastic against the complicated mold's crevices. The nitrogen is released and the plastic is removed from the mold once it has dried and taken its shape. The nitrogen injection method is critical for preventing plastic shrinkage and eliminating exterior and internal markings or strains.
Thermal Spraying – Coating
The coating is a method of applying a decorative or functional layer to a completed object that sticks to it. When it comes to manufacturing, there are a variety of coating techniques to choose from, depending on the products being produced. One of the most frequent coating processes for metals, alloys, ceramics, polymers, and composites is thermal spraying. It entails the use of a heat source and melted and sprayed coating material onto surfaces. Because of their inert status and capacity to operate as a carrier gas, Argon and Nitrogen are widely utilized in the thermal spraying process to transfer the coating material through the flame. The gases aid in the thermal spraying equipment's functioning requirements and aid in the production of high-quality products. Thus, the above are the different processes of the manufacturing of the gases that will be done accordingly to the clients' needs. Clients will be getting the best solution of customized services where they can avail the facility of the same according to their need.