75
views
views
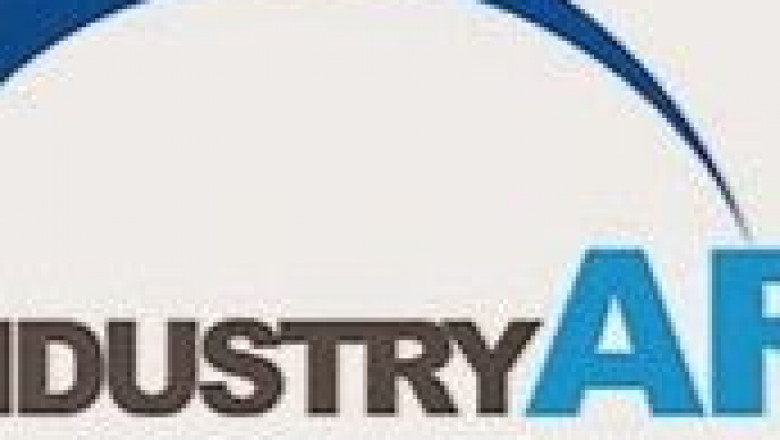
Honeycomb sandwich material Market is forecast to reach $1 billion by 2025, after growing at a CAGR of 10.6% during 2020-2025.
Honeycomb sandwich material Market is forecast to reach $1 billion by 2025, after growing at a CAGR of 10.6% during 2020-2025. The global demand for honeycomb sandwich materials has gained traction owing to its superior mechanical performance and lightweight property. Among the type of materials used for honeycomb structures, aluminum segment accounted for over one-third of the overall market in 2019, owing to its low cost and high tensile strength.
Key Takeaways
- The usage of 3D printing to manufacture honeycomb panels is likely to act as an opportunity for the market, during the forecast period.
- In the foreign industrial developed countries, the honeycomb sandwich industry is generally at a more advanced level, the world's large enterprises are mainly concentrated in the USA, Europe, accounted for most of the international market share.
- Under cyclic loading, the honeycomb sandwich materials are well known due to its low fatigue impacts which is also a major factor for the market growth.
- In addition, the use of infrared pulsed thermography or flash thermography while manufacturing honeycomb sandwich panels in space aircraft have provided various benefits, only the problem is sometimes it cannot resist heat efficiency which is not good for space aircrafts.
- Currently, due to the impact of COVID-19, automotive and aerospace industry is resulting with huge crisis, which is constraining the growth of the market.
By Type - Segment Analysis
The type segment includes Inconel, aluminum, stainless steel, and titanium. The aluminum segment includes the highest share and is driven by few factors, such as growth in automobile industry and production of aircrafts and the rise in demand for light weight and fuel-efficient vehicles. In addition, weight plays a crucial role in the overall efficiency of aircrafts. The aluminum honeycomb sandwich material offers significant opportunities in diverse applications due to its excellent mechanical properties.
By Technology - Segment Analysis
The technology segment includes expansion, corrugation, molding, and extrusion. Among these, expansion segment holds the highest share in the market by technology. In expansion, metallic sheet is cut into specified dimensions and strips of adhesive are printed on it. Adhesive is applied in such a way that adhesive prints on adjacent sheets are shifted by half of the distance between adjacent prints on the same sheet. After solidification and curing of the adhesive, HOBE block is sliced into required thickness of the core and then HOBE slice is expanded to form honeycombs.
By Application - Segment Analysis
The global honeycomb sandwich material market is anticipated to grow in the forecast period owing to driving factors such as investments in the field of satellite manufacturing coupled with increasing production of aircraft. Applicability of honeycomb structures in automotive and other end-use industry owing to lightweight attribute which helps in improving fuel economy further boost the market growth. However, the high costs of the products hamper the honeycomb sandwich material market. Nonetheless, major R&Ds for using 3D printing for manufacturing honeycomb panels is likely to offer growth opportunity for the honeycomb sandwich material market during the forecast period.
Geography - Segment Analysis
North America and Europe collectively accounted for about XX% share of the global honeycomb sandwich materials market in 2019, and is expected to maintain its dominance throughout the forecast period. This is attributed to the rise in the applications of satellites, commercial and defense aircrafts, automobiles, and trains in these regions, thereby increasing the demand for honeycomb sandwich. However, LAMEA is projected to be the fastest growing segment due to growing investments in the aircraft and satellite manufacturing industry.
Drivers – Honeycomb sandwich material Market
- Innovation in the field of material science to reduce energy consumption leads to drive honeycomb sandwich materials market.
Since 2018, the manufacturers are producing composite sandwich panels for interior structurers with low fire progression and smoke/toxic gas emission properties. As a result, the end product come up with high mechanical properties in lower cost, which will be further executed for interior applications in aircraft. In addition, the structure in honeycomb does not get affected and gets added with light weight property which will be beneficial in fuel efficient factor.
Challenges – Honeycomb sandwich material Market
- The COVID-19 outbreak impact on core industries is constraining the growth of the market.
Due to COVID-19 outbreak, various core industries are locked down, due to this, code industries such as aerospace and automotive industries have caused the great crisis in the current year 2020. The growing impact of COVID-19 have bought the production at very lower level, which as a result, have reduced the consumption of honeycomb sandwich material. The reduction in production of aerospace and automotive in the year 2020 have created huge impact, which have become the major factor that constraints the market growth.
Market Landscape
Technology launches, acquisitions and R&D activities are key strategies adopted by players in the Honeycomb sandwich material market. In 2019, the market of Honeycomb sandwich material has been consolidated by the top five players accounting for xx% of the share. Honeycomb sandwich material Market top 10 companies are Hexcel Corporation, Pacific Panels, Inc., COREX-Honeycomb, The Gill Corporation, 3A Composites Holding AG, EconCore, Samia Canada, Inc., Liming Honeycomb Composites Co., Ltd., Guangzhou Aloya Renoxbell Aluminum Co., Ltd., Benecor, Inc., and 3M Company, among others.
Acquisitions/Technology Launches:
- In June 2018, Kordsa’s composites Reinforcement Business Unit has been producing composite sandwich panels. The primary use of these panels is in the construction of galleys of commercial airplanes. Since the panels will be used for interior structures, their fire progression and smoke/toxic gas emission properties need to be very low.
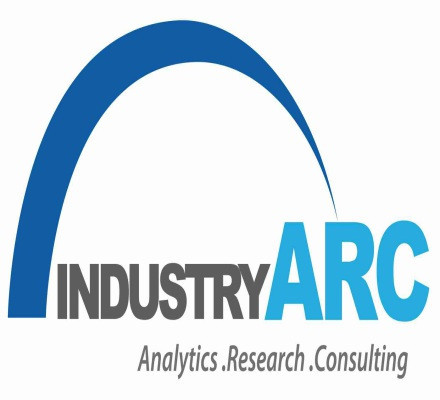