views
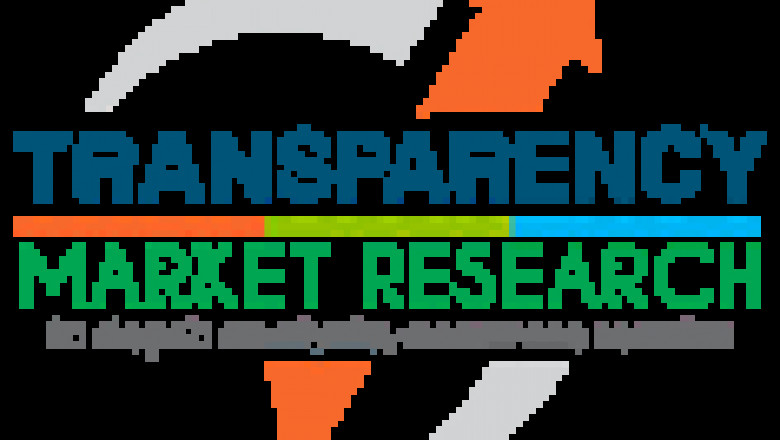
Global Bearing Isolators Market: Overview
Rising concerns over risks associated with human machine interaction in hazardous industrial and manufacturing industries and rapid urbanization are anticipated to create various growth opportunities for the global bearing isolators market in near future. Products in the global bearing isolators market provide superior lubrication solutions as well as increased protection from the harmful and unwanted external contaminants. Bearing isolators can be defined as permanent and non-wearing bearing protection devices. Installed in a wide variety of machines and mechanical equipment that feature rotating parts, products in the global bearing isolators market assist in reducing the maintenance cost and doubling the lifetime of the rotating parts in the device.
Increasing usage of bearing isolators in a huge range of end-use industries can positively influence the growth of the global bearing isolators market in coming years. Bearing isolators reduce the risk of lip seals that can negatively impact the health of both the machines as well as the workers. Products in the global bearing isolators market can also help reducing the downtime required for the replacement or repair of various machines in an industrial plant by lowering the need for maintenance and replacement. Efficiency and corrosion-free qualities of these bearing isolators can propel massive interest in the global bearing isolators market in the next few years. However, fluctuations in the prices of the raw material required to manufacture bearing isolators can challenge the growth of the global bearing isolators market in coming years.
Request Sample
https://www.transparencymarketresearch.com/sample/sample.php?flag=S&rep_id=38624
A bearing isolator can be defined as non-contact, non-wearing, and permanent bearing protection device. The device has a rotor and stator, which are bound together so that they do not separate from one another while operating the device. The rotor turns with a rotating shaft, while the stator is pressed into a bearing housing. These components interact with each other to avoid the contamination of bearing. Bearing isolators help keep lubrication in and contamination out. Bearing isolators do not need lubrication or any kind of shaft finish during operation. Bearing insulators are usually made up of bronze, which helps utilize vapor blocking feature and enables free transfer of vapor contamination at the time of rotation of the equipment. Much before the innovation of bearing isolator, the bearing protection for industrial equipment was carried out with contact seals such as lip seals and face seals. These seals were temporary and unpredictable with regard to protection of heavy duty bearings in heavy machineries. The usage of these seals led to catastrophic failures due to bearing degradation. These seals were replaced by bearing isolators. Bearing isolators have proven to be economic alternatives for lip seals and face seals, as they provide longevity and have the ability to perform extremely well with respect in providing bearing protection capability. Bearing isolators also provide two-way sealing protection for rotating equipment, which helps in extending the bearing life. Various technologies applied on high performance materials allow bearing isolators to operate far beyond the shaft speed.
Request Covid19 analysis on this market
https://www.transparencymarketresearch.com/sample/sample.php?flag=covid19&rep_id=38624
Based on type, the bearing isolators market can be divided into metallic bearing isolator and non-metallic bearing isolator. Metallic bearing isolator is usually manufactured with bronze as the standard material. Metallic bearing isolators offer excellent chemical resistance properties. Non-metallic bearing isolators are specially designed for corrosive environments. The standard material used in manufacturing non-metallic isolators is polytetrafluoroethylene. These isolators have a wide temperature capability and provide outstanding chemical resistance. The metallic bearing isolator segment accounts for the major share due to its cost effectiveness and key functional properties such as non-sparkle and high wear resistance. It is the ideal bearing isolator in oil & gas, chemical processing, metal processing, and mining industries.
More Trending Reports
Based on application, the global bearing isolators market can be split into oil & gas, chemical processing, mining, paper & pulp, metal processing, and others. Bearing isolators are primarily used in the oil & gas application, as it has proven to be the optimum solution for bearing failure. It has also helped increase the Mean Time Between Repair (MTBR) and reliability of rotating equipment in the oil & gas industry.
Based on geography, the global bearing isolators market can be segregated into Asia Pacific, Europe, North America, Latin America, and Middle East & Africa. North America and Europe are the key regions of the global bearing isolators market, led by the rise in demand for bearing isolators in end-use industries such as oil & gas, chemical processing, mining, and manufacturing & processing. Companies operating in the bearing isolators market in Asia Pacific and Latin America are investing significantly in research and development.
Prominent players operating in the global bearing isolators market include Inpro/Seal Designs, The Timken Company, AESSEAL, Parker Hannifin Corporation, The Flowserve Corporation, Garlock Sealing Technologies, John Crane, Baldor Electric Company, Elliott Group, Advanced Sealing International, Beacon Gasket & Seals Co., and Isomag Corporation. These companies hold significant share of the market. Thus, the bearing isolators market experiences intense competition.
Buy Now
https://www.transparencymarketresearch.com/checkout.php?rep_id=38624<ype=S