views
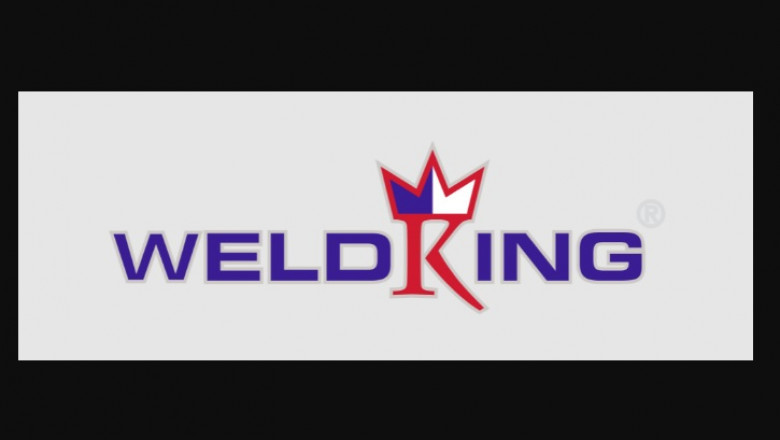
Everything about Aluminum Welder
To weld aluminum, there are a few different methods. The best method is to use a fusion-welded welder. A fusion welding machine utilizes extreme heat to melt aluminum in the desired area. It can be difficult to weld aluminum because of its high thermal conductivity. Additionally manual welding methods rely on the skills of the operator as well as the ability to use an appropriate heat sink. These methods can result in craters and poor welding. Get more information about TIG welder for sale
An aluminum welder is a useful tool when welding thin sections together. When you aim a gun at the workpiece, it is important be aware of the angle between the electrode and the workpiece. You should always point the gun toward the upward direction. This will ensure a straight and straight weld. When making the workpiece ready to be welded, aim the gun towards the heavier section. Sometimes, it is helpful to have the gun point towards the heavier section.
Be cautious when welding aluminum. An arc that's too short or too long will make it difficult to weld. To get the best results keep the gun pointed upwards and the arc directed towards the larger section. Thin sections and thick sections can be helped by a slight angle to the back. There are many settings that can be programmed into this welder and will differ according to the use. The most important characteristic is the ability to weld aluminum at high speeds.
There are a number of different types of aluminum welders. The EZ-TIG is a model that is suitable for beginners. The EZ-TIG weighs around 50 pounds in weight, has a top carrying handle and features that are geared towards novices. One of the most well-known types of mig welders is the EZ-TIG. The EZ-TIG is easy to use, requires no knowledge and can be set up at any height.
The design of the welder is important as it determines the amount of heat is released. To control the wire's speed, it must be equipped with a pedal for the foot. GMAW power supplies are typically inverter units. These are inverter-based units. Another alternative is the GMAW. This can be adjusted to alter the voltage for AC and gas. The model that can be purchased includes a built-in power source.
The Hobart 210MVP is a popular choice for professional welders. It's light and versatile. It weighs 79 pounds and is easy to move around. It also has an erect stand. The Hobart210MVP is a fantastic option for aluminum MIG welding. The versatility and ease of the 210MVP will amaze you. It's easy to maneuver and maneuverable, weighing only 79 pounds the welder is lightweight and portable.
The direction of the electrodes used by the welder must match the angle of the aluminum sheet being welded. The electrodes must be placed in a way that they are parallel to the workpiece. The unit's polarity must be uniform. Welders should not be in a position to not be able to see the weld seam. The machine must be able operate at the exact same temperature as the workpiece.
It is essential to select an aluminum welder that has the right safety features. Besides having the right gas protection, aluminum welders should also be compatible with the thickness of the aluminum sheet. You can also pick the appropriate consumable sets to fit the sheet's thickness. But, it is not recommended to go for the most expensive item. If you're looking for a more affordable model, you need to take a look at the benefits of this product.
It is important to ensure that the welder is properly set-up for the job. The welder must be able to connect to a wall outlet that is 220V. The electrodes should be the same size. A welder with an alternative size or smaller one should be compatible with the thickness of the aluminum sheet. You must ensure that your welding equipment is in the proper position when welding aluminum.
A filler chart is vital for an aluminum welder. This chart will help to choose the appropriate filler metal for aluminum. A proper welding process must be done with the proper heat inputs. An ideal welder has a better deposition rate than a manual welder. Welders should use a different shielding gas for the aluminum. A second shielding gas must be used when the welder is working with aluminum.