views
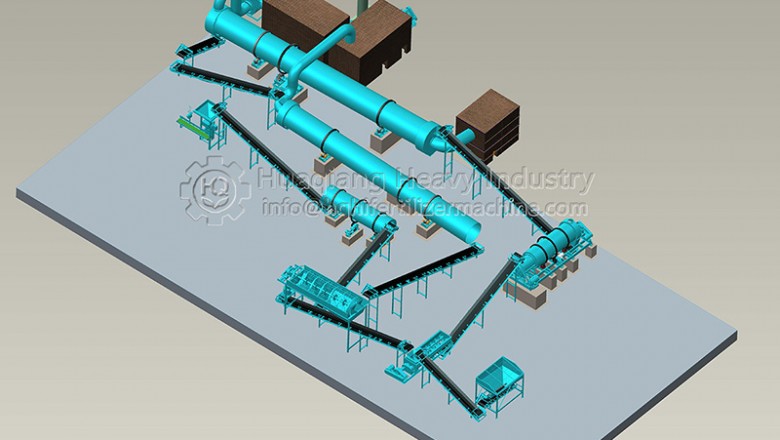
The whole process of Huaqiang NPK fertilizer production line
NPK fertilizer production line is chemical synthesis granulation, so the nutrient content of granular fertilizer is the same as the label, which can provide nitrogen, phosphorus, potassium and other nutrients to crops in proportion at the same time to ensure the balanced growth of crops.
The physical properties of the product are good, the particle size distribution of the product is uniform, and 90% of the particles are 2-4 mm in diameter; The particles have high strength, good fluidity and are not easy to be broken during transportation, storage and stacking. In the design, foreign technology is integrated to further optimize the design performance of the device.
Npk fertilizer production line process
1. Raw material ingredients: urea, ammonium nitrate, ammonium chloride, ammonium sulfate, ammonium phosphate (monoammonium phosphate, diammonium phosphate, heavy calcium, ordinary calcium), potassium chloride (potassium sulfate) and other raw materials are allocated in proportion (according to the market Demand and the results of soil testing in various places).
2. Mixing of raw materials: Mix the prepared raw materials evenly to increase the uniform fertilizer efficiency content of the overall fertilizer particles.
3. Raw material granulation: send the evenly stirred raw materials into the granulator for granulation (rotary granulator can be used, or extrusion granulator can be used).
4. Granule drying: The granules made by the granulator fertilizer production machine are sent to the dryer, and the moisture contained in the granules is dried to increase the strength of the granules and facilitate storage.
5. Granule cooling: The temperature of dried fertilizer granules by fertilizer production machine is too high and easy to agglomerate. After cooling, it is convenient for bagging storage and transportation.
6. Particle classification: The cooled particles are classified, the unqualified particles are crushed and re-granulated, and the qualified products are screened out.
7. Finished film: Coating qualified products to increase the brightness and roundness of the particles.
8. Finished product packaging: bag the processed particles, that is, the finished product, and store in a ventilated place.