views
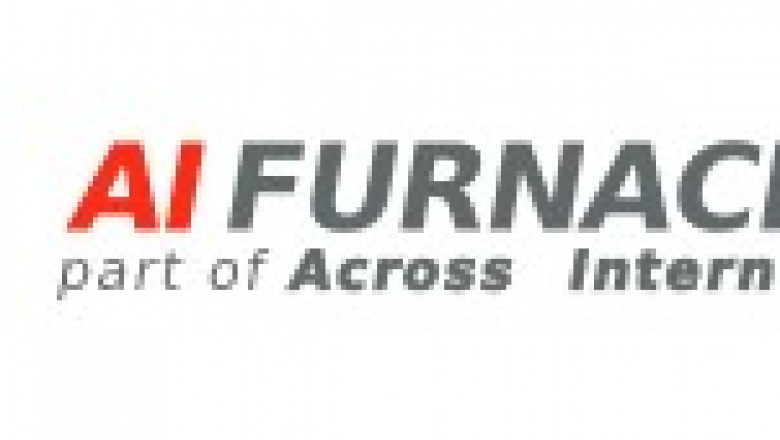
A high-temperature furnace, also known as an industrial furnace, is a laboratory heater that achieves greater temperatures than a standard incinerator. High-temperature furnaces incorporate radiant heating components inside a chamber to improve temperature control and consistent uniformity, making them ideal for many applications.
When selecting a lab furnace, its temperature range is a significant factor. You need one that can accommodate the maximum heating temperature required for the processes you conduct and the materials you’re processing. However, high-temperature furnaces can be costly.
How exactly do industries use high-temperature lab furnaces for different materials? Read on below to find out.
What is a High-Temperature Furnace Used For?
University and dentistry laboratories often use high-temperature furnaces to remove the binders, sinter or melt metal or ceramic components, and cure parts in increased heat treatments. The following industries also utilize high-temperature furnaces:
1. Metallurgy
Heat treatment methods in metallurgy may vary greatly in temperature, depending on the desired qualities of the final product. During the heat treatment procedure, the metal is held at an increased temperature for some time and then cooled again. This procedure changes the physical attributes of the metal.
A material’s mechanical characteristics are influenced by its microstructure, which is affected by high temperatures. The metal’s electrical resistance, magnetism, hardness, toughness, flexibility, brittleness, and corrosion resistance will change due to the heat treatment. Normalizing and tempering are two examples of high-temperature heat treatments used in metallurgy.
Normalizing the metals may reduce tensions induced by procedures such as welds or castings. You can achieve homogeneous grain size and content by normalizing the component. Additionally, steel is often harder than ever in any previous state after normalization.
On the other hand, tempering reduces the fragility of a metal after it becomes brittle due to the hardening process. The softer the metal product is after hardening, the more heat is required.
2. Ceramics
Commercial goods manufacturing utilizes ceramic processing, which involves heating clays and other natural raw materials to create a hardened product. Special treatment is necessary for ceramic goods made from naturally existing rocks or minerals to maintain their purity, particle size, distribution, and heterogeneity. These characteristics heavily influence the final qualities of the ceramic product.
Furnaces are used in sintering, which is done to harden the ceramic particles into a completed product after being shaped. The temperature for this burning process is vital — an incorrect firing temperature may significantly impact a ceramic’s quality and robustness. As such, ceramic labs need a high-temperature furnace that offers a wide temperature range and accurate heat control.
Additionally, a high-temperature tube firing furnace is needed for technical ceramics of the highest caliber. A well-known use of intense temperature ceramics is the tiling on the space shuttle. Similarly, you can perform glazing to create electrical insulators and tableware.
Some sophisticated ceramics may need machining or polishing to fulfill technical design requirements in high-performance applications. For instance, dental labs create ceramic dental prostheses using high-temperature furnaces.
3. Powder Processing
The term powder-metal (P/M) refers to a group of procedures that use metal powder as a starting feedstock. The metallic powders of the desired alloy are mixed using typical press and sintering P/M procedures.
To boost green strength and decrease die friction, you can include additives such as lubricants and binders into the formulation of P/M products. The green component is formed by compacting the particles after being thoroughly combined.
P/M components are often subjected to heat treatment to achieve desired toughness and other physical qualities. Quenching and tempering, case carburizing, and induction hardening are well-known methods for meeting these criteria. P/M) has become more popular recently because of its improved performance and the ability to produce near-net shapes.
4. Glass
Glass molded Europe’s cultural history, regions, industries, lifestyles, and technological advancements like no other material. For high-tech applications, either alone or in conjunction with other materials, it continues to provide cutting-edge solutions globally. Industry experts expect this trend to continue in the future.
The basic ingredients for glass — sand, sodium carbonate, ash, and limestone — are readily available and melted at very high temperatures in a furnace. For annealing, furnaces may be used to progressively cool a final product so that the glass doesn’t shatter.
Heat treatments also improve the resilience and strength of glass goods. Heat-strengthened and tempered glass are two types of heat-treated glass.
Creating the Perfect Furnace
Drying, heating, cleaning, thermal treatment, and more can benefit from laboratory furnaces. There’s a broad range of furnaces available, each suited to a specific purpose, so you need to consider several variables when choosing a laboratory furnace.
Consider the capacity (liters), the temperature ranges (Celsius), the intended application (indications), and the steps to use. It can only be a wise investment if your laboratory can use the equipment.
If your lab is ready to leverage the multiple applications of a high-temperature furnace, make sure to trust only reputable lab furnace manufacturers. Check out AI Furnaces’ high-temperature lab furnaces now!