401
views
views
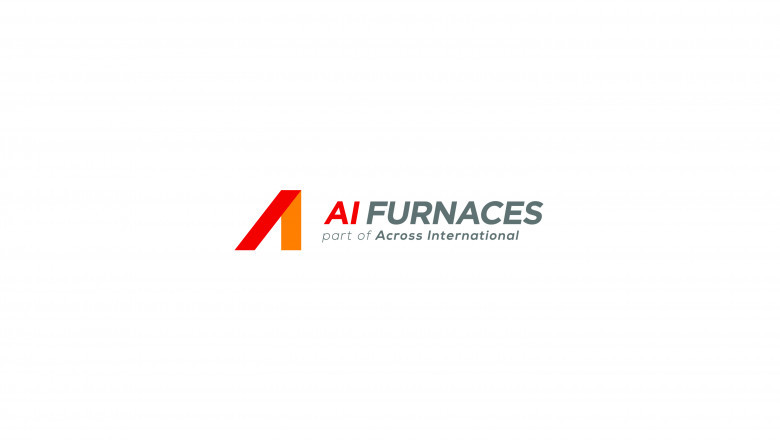
We manufacture High-Quality Lab Furnaces and Ovens to perform and control heat treatments. Tech proudly serves our customers with a 100% satisfaction guarantee.
What is Vacuum Sintering?
Advantages of Vacuum Sintering
- Reduces machining processes
Vacuum sintering helps manufacturers create special-shaped components, so the output is already close to the end product’s final shape. This minimizes the need for post-machining processes, saving you time and labor.
- Prevents atmosphere contamination
This process involves gasses that help deoxidize and remove non-metallic substances from raw metals. This process prepares materials for assembly, heat treatment, densification, and finishing.
- Cleans and brightens components
By cleaning and deoxidizing raw metals, both the debinding and vacuum sintering processes help create brighter and purer materials by removing defects, surface flaws, and dimensional inconsistencies.
Picking the Right Process Gas
- Nitrogen
Nitrogen is the most used gas for sintering because it’s less expensive than other gasses. It also provides more flexibility to sintering atmosphere systems, making it easier to turn furnaces on and off and keep them idled under protective environments.
- Argon
Argon is more expensive compared to nitrogen and is only used as an inert gas when the workpiece material is sensitive to nitrogen. It also helps protect molten and heated metals as they’re processed.
- Hydrogen
Hydrogen is used as a reducing agent in the sintering process. It helps protect sintered metals from oxidation and decarburization and enables consistent performance throughout the process. However, it comes with a hefty price, like argon.
How to Choose a Vacuum Sintering Furnace
- Cleaning process
Since metals have to undergo the debinding process before being placed in a vacuum atmosphere, you must determine whether you need separate furnaces to handle each treatment or just one to handle both.
Vacuum sintering requires metals to be clean, meaning it needs a furnace that’s also free from substances that can negatively affect the product’s characteristics. If your binder is difficult to use or your application requires a higher-than-average purity, you may need to use separate furnaces for debinding and vacuum sintering.
Meanwhile, if you plan to use a single lab furnace for both treatments, make sure it uses gas-flow distribution with a box separating the binders from sintering powders.
- Fragility of parts
Choose a furnace capable of reaching the required temperature for pre-sintering, as this process can help strengthen materials after the debinding process. Debinded materials become fragile and at risk of breaking when moved from one furnace to another.
- Manpower
If you’re short of workers, a single furnace for debinding and vacuum sintering may work in your favor. Using a furnace for both treatments can help you meet high production requirements where you may need to work overnight to process raw materials.
- Productivity
Many factors come into play when choosing a furnace based on your capacity. Do you have high or low production requirements? How long do both the debinding and vacuum sintering processes take? How many loads would you usually transfer from one sintering furnace to another?
Answering these questions can help determine if you need a separate furnace for each treatment or if a single one will do.
- Energy consumption
Minimizing energy consumption is an important part of any manufacturing process today as it helps reduce costs and save the environment. If saving energy is part of your goals as a manufacturer, you may want to consider getting a single furnace for debinding and vacuum sintering.
However, remember that the amount of energy used for debinding can be different from that for vacuum sintering. Make sure to research how much energy each treatment uses to determine the right furnace for your needs.