views
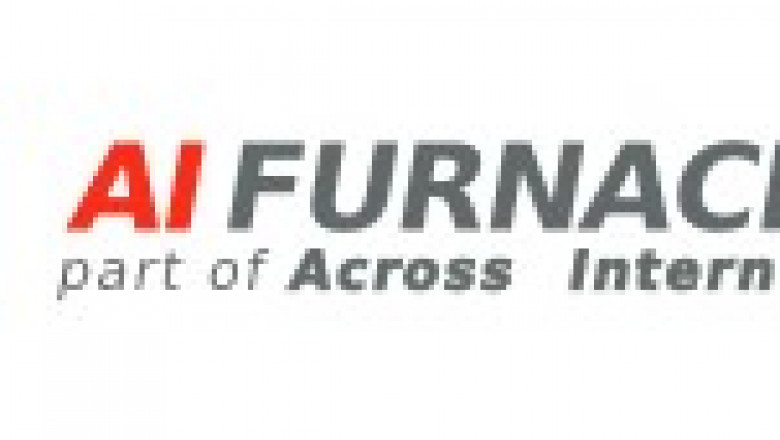
Advanced ceramics pertains to products created from high-purity, inorganic mixtures using specialized manufacturing methods. These are highly absorbent, magnetic, conductive, and insulating, making them excellent alternatives to traditional materials like glass, metal, and plastics.
Due to these qualities, advanced ceramics are utilized in the production of electronics, medicine, transportation, and other industries. Much like traditional ceramics, advanced ceramics are created by firing precursor powders using extremely high temperatures.
This article will discuss how industrial ceramics are made through high-temperature firing and their common applications.
The Role of Firing in Ceramics Production
Ceramics production is a highly technical manufacturing method involving precise heating temperatures. Failure to observe the right firing conditions can drastically impact the quality of your final output.
The firing process hardens the ceramic, making it more durable and eliminating all carbon and sulfur compounds. Removing these elements is essential as they can make the product structurally weak.
Firing ceramics also eliminates water—advanced ceramics tend to retain a certain percentage of water even after bone-drying, and the firing process eliminates traces of moisture. However, prematurely taking the water out can create steam, breaking the clay pieces while still firing in the furnace.
Another thing you should consider is the ceramics’ tendency to expand 1 to 2% during firing and contract by 1 to 2% during cooling. If you rush the heating and cooling process, it will cause the clay to crack, an occurrence known as dunting. You can easily see signs of dunting as clay pieces will be warped and consequently not fit together.
Temperature plays an integral role in the firing process to achieve the desired outcome. A few degrees off the proper temperature can cause defects like discoloration or compromise the product’s hardness.
Utilizing advanced ceramics in production requires you not only to subject them to proper heating conditions but also to secure the right equipment for the process. It’s best to use a high-temperature furnace to make sure that your equipment can create the conditions necessary to achieve the desired properties in the final output.
Important Properties of Advanced Ceramics
Advanced ceramics have unique properties that make them ideal for different scenarios.
- Heat Resistance
Advanced ceramics can withstand high temperatures and retain their function and shape due to their low thermal expansion, low thermal conductivity, and high thermal capacitance.
Ceramics formed using aluminum metals begin degradation at 660°C, while alumina starts at 2,000°C. Temperatures like these are well above the melting point of metallic materials.
- Thermal Shock Resistance
Temperature fluctuations tend to cause thermal stresses to traditional ceramics, propagating micro-cracks that permanently damage the material. Fortunately, advanced ceramics are highly thermal-shock-resistant. This means they can withstand sudden changes in temperatures of up to 550°C with no adverse effects on their properties.
- Conductivity
Using advanced ceramics in creating specific components affords manufacturers flexibility. This is due to varying advanced ceramic materials offering low or high thermal conductivity values.
Those seeking advanced ceramic materials with low thermal conductivity can refer to zirconia. Alternatively, aluminum nitride is ideal for those looking to capitalize on high thermal conductivity.
- Insulation
Advanced ceramic components are often used to create various surface-mounted electronic parts in navigation systems and mobile phones because they do not conduct electricity.
Advanced Ceramics Applications
Different industries utilize industrial ceramics for various production processes. Here are prime examples of their role in different sectors.
- Dentistry
Innovations in industrial ceramics are vital to dental labs to create reliable dental-restoration solutions. Advanced ceramics are used to create dental bridges and permanent porcelain dental parts. Extruded ceramic composites undergo extreme heating, reaching temperatures as high as 1,120°C.
Maintaining this heat is vital to ensure the product will not shrink or distort once moisture from water is removed and the porcelain bonding begins.
- Surgical Implants Industry
The surgical implant industry uses high-temperature lab furnaces to create its products. Advanced ceramics’ heat resistance can withstand the necessary temperatures to sinter pure alumina powder, one of the main components of surgical implant production.
- Electronics
Due to advanced ceramics’ versatility, they are often utilized in producing various electronics. Products like advanced ceramic heat sinks provide the right climate for high-power electronics and can function as active or passive components, depending on the application.
- Aeronautics
Advanced ceramics are lighter compared to most metals and stable at higher temperatures than high-grade technical plastics. Thus, the aeronautics industry uses advanced ceramics to reinforce their thermal protection systems and insulate tiles for their engine components.
Create Advanced Ceramics with the Right Furnace
Extremely high temperatures play a significant role in the creation of advanced ceramics. They eliminate various impurities and ensure the product’s durability. With firing being an integral part of advanced ceramics, it’s equally important to secure the right furnace with the right features and settings.
If you’re looking to secure high-temperature lab furnaces, look no further than AI Furnaces. An industry leader in manufacturing heat treatment, laboratory, and material processing hardware, AI Furnaces offers high-quality and innovative lab ovens and furnaces. For further inquiries regarding our various lab furnace offerings, contact us today.