views
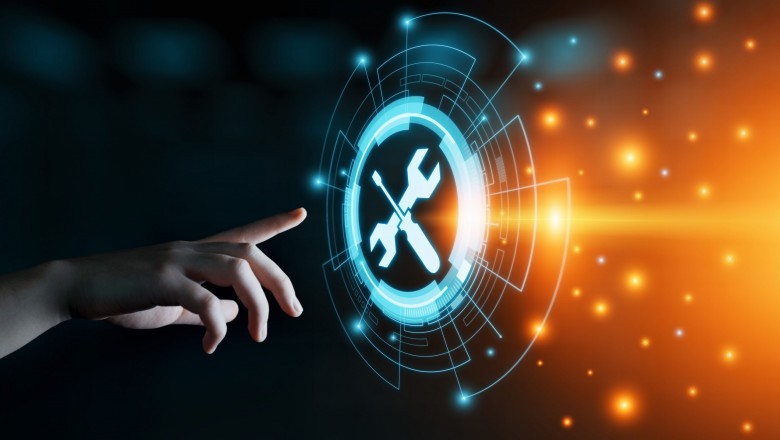
Predictive maintenance systems are designed to assist manufacturing companies in determining the condition of their on-site equipment so as to gauge when regular maintenance ought to be done. This system promises significant cost savings since tasks are done only when necessary, thereby aiding in growth of the predictive maintenance market. The software can detect components that may prove to be faulty and thus prevent them from causing costly breakdowns. Moreover, the programs come with easy-to-use modules that make maintenance jobs easy, safe, and effective. These programs also help in ensuring optimal performance of the machinery by identifying possible problems in real-time and acting accordingly.
The demand for Predictive Maintenance Management (PMM) program is high in the predictive maintenance market for ensuring smooth operations. A robust PMM program consists of several features. It starts off with an evaluation of a company's condition monitoring system. Such a system is usually based on data obtained during the equipment's life cycle. The program then determines how much maintenance is needed to keep the equipment running smoothly and how to reduce costs involved.
The initial step towards an effective predictive maintenance products in the predictive maintenance market is to determine the nature of each piece equipment or facility. Factors that have a bearing on such a procedure include current operating conditions, anticipated failures, existing or projected service history, and expected failures in the near future. The software can then be trained to detect such factors and apply recommended solutions to reduce costs and improve efficiency. Several applications exist for using condition-monitoring applications in manufacturing facilities. Some of these applications are discussed below.
A common use of a PMM program is in the case of spare parts. Spare parts can be expensive to buy from distributors, and many times they need to be replaced after a very short span of time. In such cases, PMM products in the predictive maintenance market can identify trends that indicate the presence of spares, determine when they will be needed most, and can be adjusted accordingly so that the supply of spare parts is not in surplus and so that the required downtime is minimized. As such, with this application, the PMM can forecast the number of production hours needed for the replenishment of spare parts and can thus provide information that is crucial in production planning.
Another application of PMM is in the area of cost savings. Cost savings can result from many sources, including improved manufacturing processes, improved equipment, and reduced labor costs. In certain circumstances, cost savings can result from the reduction of required repairs or disruption of operations. To address such issues, a Predictive Maintenance Management system can analyze data analysis of operation costs and make recommendations as to the most cost effective preventive maintenance practices.
Read More @ https://digitalinsightscmi-blog.blogspot.com/2021/07/demand-for-predictive-maintenance.html