views
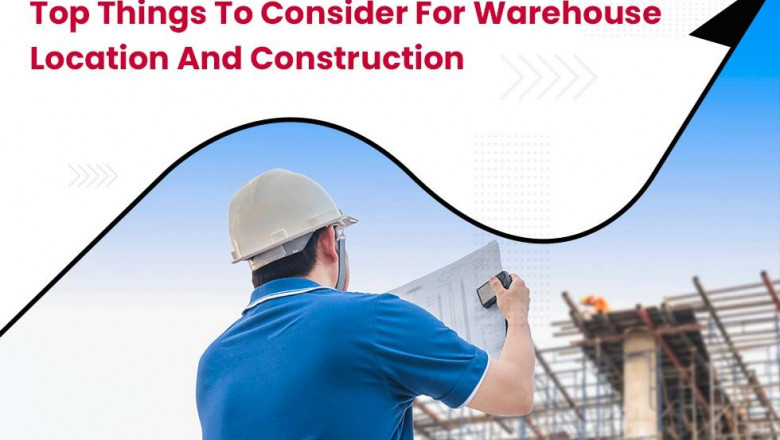
Top Things to Consider for Warehouse Location and Construction
A warehouse is an indispensable part of every supply chain network, regardless of what the product, be that as it may, its location is critical as well. This is because it can help with lessening the order fulfilment time, exertion, and expenses. It further ensures your company’s ability to effectively and profitably serve your customer.
What is the Main Purpose of a Warehouse?
Warehouses are basically a logistics system that a company uses for the storage of raw materials, agricultural produce, or finished goods until their distribution for sale.
Once you start planning to construct your new warehouse, the unknown factors can be daunting and you’ll have many warehouse selection factors to consider.
Let us explore the following warehouse location procedure that will assist you with picking the most ideal site for your facility:
1. Physical Location
The site of your warehousing center is essential to your business’s long-term success. Although there is not a “One Solution Fits All” when deciding where to locate and engage a warehouse, the location you choose should help you increase the efficiency of your warehouse’s supply chain.
2. Accessibility
Picking your warehouse location strategically will affect your accessibility to your customers. A warehouse should be situated in such a location where it expands the overall efficiency of the supply chain of the firm, and in no way creates a setback in the shipment cycle.
Blocked streets, bad signaling, and highways can skyrocket the accident rates and fuel consumption and are tedious. This dilly-dallying can raise transporting costs, and adversely affect the synergies with the customers.
Further, consider the following points with the transportation of products, be it to or from the warehouse:
- Accessibility to highways and exit ramps
- Access to public transportation
- Highway interconnectivity
- Average traffic volume and speed
- Traffic peak hours
- Road safety and conditions
- Proper road signs and signals
3. Local Demographics
Another essential aspect to consider while making decisions about warehouse location is to ensure that you are close to skilled labourers in the local job market. Do the workers are competent to handle the products? Do the services and setup come at a sensible cost for the organisation?Considering these factors while finding a location for your warehouse can reduce the cost of training and ensure high productivity levels. When the location has a demand for skilled workers, you could be spending more on operating costs and more significant compensations.
4. Layout Design and Flow of the Facility
It means quite a bit to think about the design of your warehouse to pave the way for optimal productivity levels. For example, if you hold volumes of stocks, you might encounter more traffic than a specialty retailer. In such a case you need an expanded storage area with ordering units clearly defined so that products can be moved out of the way whenever required. This is what we call day-to-day flow.
5. Size and Capacity
You need to choose a warehouse that meets all your business’s specific needs, including the capacity and infrastructure. A lot of undesirable fiascos can be avoided by being proactive and checking the storage necessities of the warehouse location.
6. Environmental Conditions
When picking a warehouse site, the local weather condition is likewise an essential factor to consider. You may find a facility at a lower rental however it’s crucial to find if the location is prone to natural disasters.In case your warehouse facility produces too much noise, it may not be a good addition to the community near key schools and neighborhoods, since these disruptions could affect them adversely. In case your business deals with harmful material, choose an isolated area where there are no residences to ensure no harm or mishappening.
7. Supply Chain Partners
While picking the best location for your warehouse, choose the one easily accessible to your supply chain partners. This will help in preventing delays in product conveyance times and will reduce transportation costs. Also, if you’re importing merchandise from suppliers abroad or exporting them, an ideal warehouse site should be accessible to nearby ports.
Conclusion
Whether you are relocating or constructing a new warehouse for your business, choosing the right location is a crucial decision as it can make or break businesses. If you’re looking for the best location for your warehouse NimbusPost is at your service. Store your inventory near your customers & reduce delivery timelines while increasing your profit margin.