views
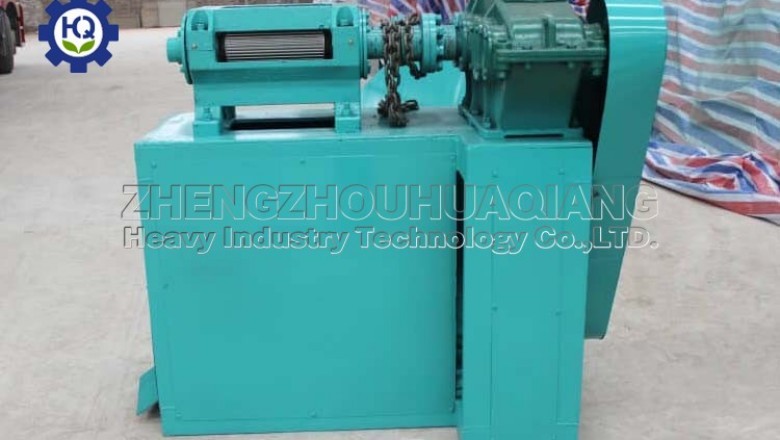
What's the advantage of using dry double roller granulator
Dry double roller granulator is a kind of dry rolling technology, which compresses powdery materials with water content less than or equal to 5% into flakes or lumps, and then through crushing and screening process, the flakes and lumps can be turned into granular materials that meet the use requirements.
Product details:
Powder granulation technology as a main branch of powder process processing, with the improvement of environmental protection demand and production process automation, its importance is becoming increasingly prominent. Granulation of powder products has become an inevitable trend of powder post-treatment technology in the world. The significance of particle strength processing for powder products is mainly reflected in three aspects
1、 Reduce dust pollution and improve working conditions.
2、 To meet the production process requirements, such as increasing porosity and specific surface area, improving heat transfer and so on.
3、 Improve the physical properties (such as fluidity, air permeability and bulk density) of the product, avoid the adverse effects of segregation, pulsation, caking and bridging in the subsequent operation process (drying, screening and metering) and use process (metering and batching), reduce pollution, improve appearance, improve fluidity (by organic fertilizer granulation machine), facilitate storage and transportation, control solubility, control porosity and specific surface area, etc It creates conditions for improving the automation of production and use process and closed operation.
Dry opposite roller fertilizer granulation machine adopts dry rolling technology to compress the powdery material with 5% water content into flakes or lumps, and then through crushing and screening process, the flakes and lumps can be turned into granular materials that meet the use requirements. Dry rolling granulation mainly relies on external pressure, so that the material is forced to pass through the gap between two relatively rotating rollers and compressed into pieces. In the rolling process, the actual density of the material can be increased by 1.5 ~ 3 times, so as to meet the specified particle strength requirements.