views
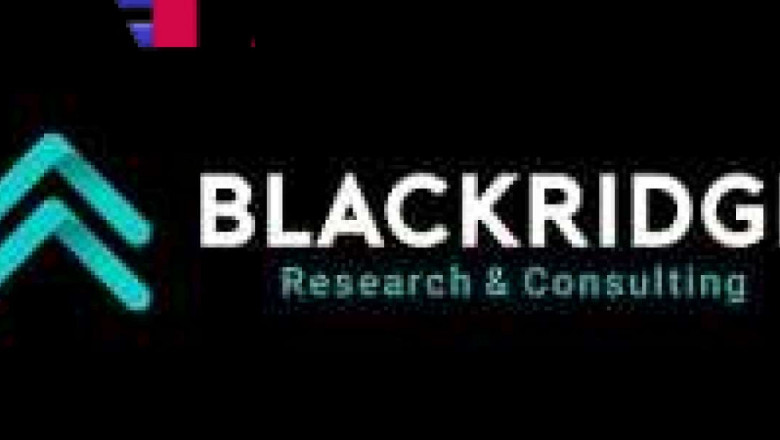
Lean construction is a holistic approach to combining operational research and practical development in the construction process. The adoption of lean construction principles or LC principles allows for continuous improvements in the end-to-end designs of construction projects.
It can be a game changer in the construction industry as it aligns every aspect of the construction process, from design to construction, maintenance to recycling. Waste reduction and value creation for the end users being the primary objective of the lean construction method, lean production has swiftly gained popularity all over the world.
This article explains what lean construction is and how lean construction principles can be implemented for mega construction projects.
This article will cover
The need for lean construction
Robust progress tracking system
Staff mindsets and capabilities
Main principles of the lean construction method
Benefits of adopting LC principles
Implementing lean construction for infrastructure projects
1. Create values for end users
2. Identify value stream processes
3. Prioritize continuous workflow
4. Leverage pull planning and scheduling
5. Continuous monitoring and optimization
Examples of Lean Construction Projects
What is lean construction?
Lean construction is an iterative approach to designing and building. The lean practice involves planning, designing, and executing in smaller chunks, similar to modular construction practices. With the constituent units being designed and built one at a time, the lean methodology allows the construction team to create definitive workflows.
Furthermore, the project owner can expect more value out of the project as the modular building method leads to minimal waste reduction. The method is also inspired by the planner system, where multiple planning tools are used simultaneously to help a construction management team keep track of its time, appointments, and workflows.
Rather than performing all of the planning and design upfront, work is planned, designed, and scheduled weekly and continues to increase gradually as lean manufacturing progresses.
The need for lean construction
A study by Aalborg University in 2021 found that more than 80% of infrastructure projects go over budget. The cost overruns were more than 40% in almost a third of these projects.
Infrastructure projects in remote and inaccessible locations often suffer from roadblocks due to unforeseen difficulties. Even the best-laid plans are likely to fail. The ground-level difficulties often expedite due to skill shortages.
As a result, many companies have responded to these challenges by rethinking how large capital projects are planned, managed, and executed. They have resorted to applying the same lean principle that propelled productivity and quality in the manufacturing sector.
The lean project delivery approach aims to optimize variability in the construction process. Here is how lean construction is applied by three core changes in the traditional construction processes.
Efficient interaction model
Modern construction projects are often complex and require the involvement of multiple stakeholders. Therefore, project owners utilize the services of EPC contractors to deliver complete construction projects to minimize risks from their end. However, even after employing contractors, project owners still pay for risks. And this happens due to a lack of decision rights to implement changes when required.
This practice can be changed by incorporating better project delivery methods in the construction sector where owner-contractor interaction is robust and timely. Lean construction practices can build the interaction model required to efficiently complete large-scale projects.
Robust progress tracking system
The on-site activities are too scattered for large projects in the construction sector, making it difficult for the parties involved in the construction process to get a clear picture of the work progress. This is true, particularly for the General Contractor and other middle managers working on the ground. This lack of clarity can lead to problems being discovered too late, aggravating their effects.
Therefore, a robust progress tracking and performance management system can transform the project, making it more transparent. By employing the lean method of construction, project owners can set some straightforward metrics. One such metric is measuring compliance with the construction schedule and risk.
Staff mindsets and capabilities
The skills and capabilities of the front-line staff and their supervision play a crucial role in project management. However, construction managers can’t just assume that enough people with the right skills and capabilities will always be available, especially for remote or developing regions.
That is why lean management demands other skills besides diligent planning and a capable workforce - apt construction technology, to stay immune to unforeseen events.
Main principles of the lean construction method
The idea of lean was pioneered by Toyota, thereby gaining the name of the Toyota Production System principle. Basically, this principle offers a lean, clean, efficient, and safe working environment for everyone involved in a particular task. The lean principle is associated with Kaizen - a Japanese word for continuous improvement. The Kaizen approach advocates for continuous improvement as the work progresses. Even the smallest change can initiate a chain of positive changes, ultimately improving a task's output.
The lean philosophy is based on the 5S principle, which can be briefly summarized as follows:
- Sort – Sort everything at workplaces. Get rid of surplus items like tools, documents, materials, or other inventory.
- Set in order – Mark the specific places for specific objects. This will ensure everything is at the disposal of everyone and no time is wasted searching for anything.
- Sweep – After a task is complete, make the work site tidy. This will allow others to work without obstruction.
- Standardize – This principle involves clearly defining the scope of work and devising standard practices for everyone.
- Sustain – After successfully implementing the first four principles, a team should adhere to them.
Adopting lean practices
The lean manufacturing culture is highly employee-focused. Any company wanting to incorporate lean principles depends greatly upon its employees. After all, employees spot hidden issues and deal with them. Moreover, they are responsible for waste reduction and work more efficiently.
However, this adoption of the lean working model is impossible without well-coordinated teamwork. In this respect, the company has to first set a common goal for the entire team. When the team has a common goal, the teamwork will be more solid, and the adoption of lean principles will be possible around the common purpose.
When it comes to the construction sector, a lean working model is extremely important because the work environment in the construction industry is highly diverse, with different teams simultaneously working on different parts of the same project. Therefore, a coordinated teamwork approach is necessary to streamline the entire work process and achieve the common objective of completing the project within the timeline and budget.
Benefits of adopting LC principles
- Adopting LC principles leads to the use of fewer construction materials and less waste creation which ultimately reduces the overall costs.
- The principles encourage diligent project planning that reduces construction time.
- Onsite contractors can minimize accidents and maintain a high safety rate.
- Better scheduling and predictable workflows
- Better communication between different construction teams
- Well-coordinated cooperation among teams
- Low chances of cost overruns and project delays
- Improved worker productivity and minimal waiting time
- Managers can expect better worker accountability
Implementing lean construction for infrastructure projects
The majority of large infrastructure projects frequently suffer from cost overruns and delays. Managing and overseeing such large-scale projects is often challenging for both the general contractor and the construction company. As the complexity of the project grows, there is lower productivity and less profitability for the stakeholders in the infrastructure project.
It is time for construction professionals to capitalize on the advantages of lean construction. Implementing lean principles in infrastructure projects can boost production and profitability.
Here is how applying lean principles can elevate the profit and quality of the project.
1. Create values for end users
Contractors and subcontractors involved in projects need to focus more on value creation. They must ensure that the project’s resources, including the materials and information, are linked together. This will create a single workflow which will ultimately streamline the disjointed works.
When implementing lean principles for infrastructure projects, the project management team can substantially reduce downtime and ensure every activity for the project adds value to the overall project.
To implement the lean principle, project teams can divide the whole project into various sections. Thereafter, they can design a workflow based on every subcontractor’s contribution. This workflow will help concurrent tasks undertaken by different subcontractors to proceed in a streamlined manner.
2. Identify value stream processes
In simple terms, the value stream is anything the client values or anything that adds value to the project from the client’s perspective. Once a project team identifies the necessary processes required for the value stream, they should be mapped carefully.
This mapping will determine what activities are essential and what should be completed on priority. Also, take stock of the labor, materials, and information needed for each value stream activity. Any process that isn’t valuable for your client can be eliminated.
Reducing waste: Reducing waste is one of the important aspects of lean construction. High waste generation can result in increased expense as waste disposal needs man and resources. Besides, it can also delay the project since the site needs to be cleared off for new activities.
Defects: Anything that is not done properly needs to be done again; thus, it can be termed defects. This rework results in a waste of time, resources, and productive hours. Therefore, meticulous project planning can save all these from being used again.
Waiting time: This time is often wasted as workers are stuck waiting for materials to be delivered onsite. In other instances, they wait for other teams to finish the work. This waiting time disrupts the complete construction workflow and results in the loss of productive hours.
Underutilization of human resources: This happens when the wrong professionals are hired, and people are assigned tasks that do not fit their merit and skillset. As a result, the work will not be proper and can lead to either defects or loss of inventory.
Inventory: Inventory refers to all the materials that are required for the construction process to complete smoothly. Since lean construction methodology involves modular construction and progresses week to week, the inventory should be enough to complete the construction of a particular week. There is no need to horde inventory by occupying space. This will allow other teams to work parallelly to finish their part of the construction.
3. Prioritize continuous workflow
Lean construction aims to produce a continuous, consistent, and predictable construction workflow. Each stage of production is completed in order. For example, you wouldn't begin installing drywall in a room until all the electrical and plumbing had been installed. All parties must communicate and collaborate proactively to eliminate disruptions and promote flow.
You don't want employees waiting for employment or vice versa. Contractors can ensure they have the capacity to complete their part of the work on time by dividing a project into discrete production zones. If a stage of production falls behind or ahead of schedule, it is critical to communicate with others to minimize its impact on others' workflow.
4. Leverage pull planning and scheduling
The planning and scheduling in lean construction management is termed pull-planning, which is basically reverse planning. Pull planning starts backward, starting with the end process in mind and defining the backward steps incrementally.
Pull planning helps identify priority works and schedule them in a sequence per their degree of priority. Every activity is scheduled based on downstream demand to keep the workflow going without disruption. Since all the works are completed sequentially, the completion of one task initiates the next task.
Subcontractors are typically responsible for accomplishing the tasks per pull planning and scheduling. Therefore, all the subcontractors need a dynamic and resilient communication and collaboration mechanism to schedule their tasks.
5. Continuous monitoring and optimization
The key ideas of lean construction are waste minimization and continuous improvement. The chances for improvement are recognized and addressed by real-time task monitoring and applied to future building projects for improved outcomes.
As a result of continuous improvement, lean construction achieves the following advantages:
- Enhanced safety
- High-quality construction
- Improved productivity
- Reduced waste
- Better risk management
- Fast-track project delivery
- Greater customer satisfaction
- Maximum returns
Continuous improvement results from the purposeful and consistent use of lean concepts. These concepts are based on the lean thinking that a construction firm can only attain greatness if they constantly try to learn, grow, and optimize its operations.
The construction crew can be more efficient and productive as a result of adopting this comprehensive lean approach, thereby making building projects more economical and profitable. Moreover, the lifecycle of any construction project will be longer since the value stream is intricate.
Examples of Lean Construction Projects
- The ISTB (Interdisciplinary Science and Technology Building) in Arizona, USA, is a real-life example of a lean construction project. The building combined lean construction with BIM (Building Information Modeling) for continuous improvement during construction and saved USD 2 million while completing the work in 16 weeks.
- Sutter Health is another example in North California, USA. The not-for-profit hospital system serves over 100 communities in the region. To do so at scale, the hospital system leveraged lean construction principles, including IPD (Integrated Project Delivery), to expand aggressively into other communities within a decade.
- T-30 Hotel in Hunan, China, is another example of a blend of modular construction methods and Lean construction methods. The 30-story hotel, spread across 183,000-square-foot, was constructed by 200 workers in just 15 days.