views
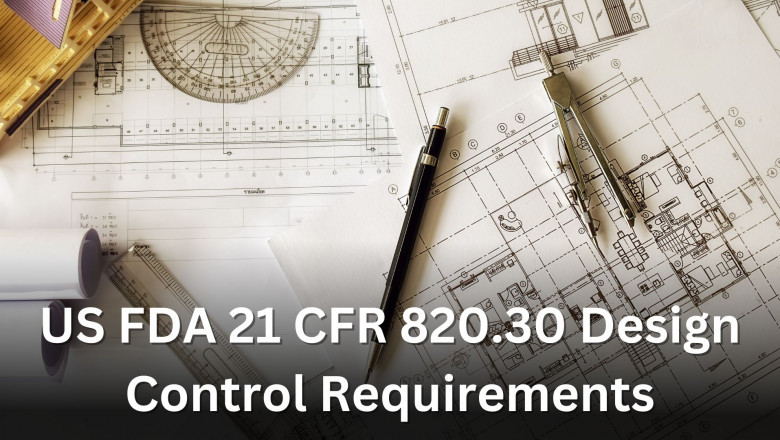
Information about US FDA 21 CFR 820.30
What's FDA Design Control?
Design controls are defined as an interrelated set of practices and procedures incorporated into the design and development process. FDA design controls make a methodical assessment of the design an integral part of development. With design control, any scarcities in design input requirements or disagreement between the proposed designs and requirements are detected beforehand and corrected immediately in the development process. Design controls intend to increase the chances of transferring the design to product, without much difference, into a device suited for its intended use.
Design control isn't a new conception, or indeed a new requirement, but a longstanding tradition in medical device manufacturing. Since 1990, the FDA has demanded medical device manufacturers misbehave with the criteria outlined in 21 CFR820.30. These requirements aim to insure medical devices retailed in theU.S. match applicable standards and address the needs of cases and other users.
At the design stage, an figure design control process should be started and actualized as a point of the Quality System demand. Generally, figure design controls are straightforward and logical way to insure that what you develop is what you meant to develop and that the last item lives up to your customer’s requirements and solicitations.
Operon Strategist the leading medical device regulatory consultant providing consultation for 21 CFR 820.30 design control with extensive experience and the practical implementation of design controls regulation for developing new design control processes or for making improvements to existing processes. We assist in design controls as per FDA and ISO 13485:2016 that can be mapped to the process that works best for the organization and the product being developed. If you need any help setting up a design control system, or wish to modify an existing system in order to align with ISO 13485 or FDA design controls, please contact us.
For medical device design, the US FDA is interested in what's the final finished medical device and the process that led the manufacturer to the final design of the device, the device design process. Specifically, FDA wants manufacturers to insure that the original user requirements are met by the final finished medical device. To insure manufacturers are designing products that meet user requirements, FDA requires medical devices to be designed according to design controls, as regulated under 21 CFR820.30. Design controls regulations are a set of conditions that allow manufacturers to control the way a device is developed.
We've experience with each constituent part and the GMP regulations that together form the base for their development and manufacture medicine Device Combination Products( FDA 21 CFR part 820) and( 21 CFR Part 4).
The Benefits of Effective Design Control
The benefits of effective design control impact manufacturers as well as cases. Robust design control improves product safety, performance, and overall product quality. Process effectiveness shortens cycle times by providing quick access to crucial tasks and approvals. A guided- yet-flexible workflow improves the end- to- end process and provides control and consistent execution of tasks without duplicating effort.
Effective design control also enables manufacturers to avoid potential compliance issues because all records, frompre-market design topost-market data collection and design change, arecross-referenced in one integrated system. Manufacturers can demonstrate that a controlled and documented process is in place and has been executed properly.
Eventually, effective design control ensures all design, quality, and nonsupervisory data is examination ready. This factor eases the burden on manufacturers when preparing for checkups and helps reduce errors and inspection findings.
What Are FDA Design Controls for Medical Devices?
The design control process follows a set of practices and procedures that help medical product developers
Manage quality.
-
Manage quality.
-
Ensure each product meets all requirements.
-
Prevent potential issues or recalls in the future.
FDA Design Controls
Design controls for medical devices are regulated by the FDA under 21 CFR820.30. They must be enforced by manufacturers of class II or III medical devices( and some class I devices).
FDA Design & Development Planning How to Do It
How are you going to go about designing & developing your device? Design and development planning covers exactly that.
According to section820.30( b) of the FDA guidance, design and development planning requires:
-
Each manufacturer shall establish and maintain plans that describe or source the design and development conditioning and define responsibility for perpetration.
-
The plans shall identify and describe the interfaces with different groups or conditioning that give, or affect in, input to the design and development process.
-
The plans shall be reviewed, streamlined, and approved as design and development evolves.
Read more articles -