views
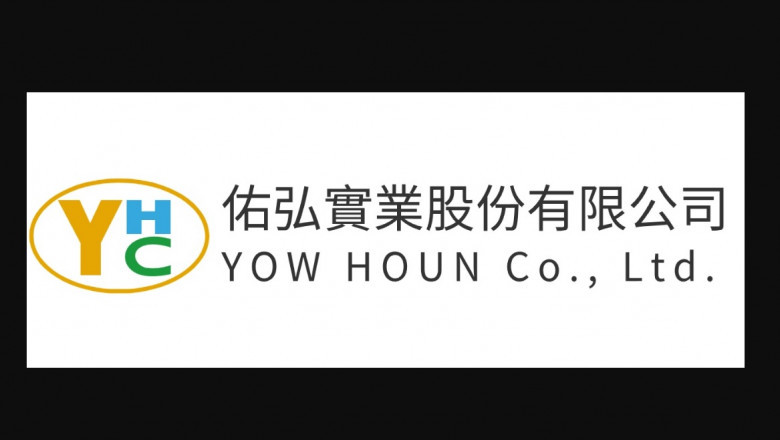
Plastic Injection Molding is an excellent method for creating parts with intricate designs. This process removes the need for additional operations such as core pulls and threading fixtures, which can lead to a reduction in time to produce and costs. Plastic injection molding is much cheaper than CNC machines used for machining parts. In addition, it could save a company cost on materials since it doesn't require the large-scale manufacturing processes that are that CNC machines require. Continue reading to find out more about Plastic Injection Molding. Get more information about OEM Plastic
An injection molding process begins with an injection of raw thermoplastic material. The material is then placed in the barrel, which has been heated to a certain temperature. This temperature increases the amount of space between molecules, which in turn reduces viscosity. This allows the polymer to move freely through the injection unit. Then the raw material is directed towards the unit by the screw. This screw reduces heating time by mixing and homogenizing plastic's viscous properties and thermal distributions.
The process is quite simple. The plastic pellets are inserted into the barrel, and then melted through friction between the rotating screw & the barrel. To close the mold by pressing the two halves together under hundreds of tons of pressure. Then, a screw that is rotating moves to a predetermined distance and then injects the specified amount of molten plastic in the mold. The molten plastic cools , and conforms to mold design.
Plastic Injection Molding's goal is to produce parts with a low wall thickness, a low volume, and minimal undercuts. These characteristics allow for faster cooling times and less costs for tooling. Injection molding is carried out in a mold that includes a clamping device and a corresponding mould. This machine requires various controls, such as clamping force, ejection and opening and closing of mold plates.
Injection molding is a versatile and efficient method of making plastic parts. The mold maker develops a tool for the process, which contains the required geometry and features. The mold is then filled with the molten plastic and then it is then cooled to form. The mold can be used again to create similar products. The result of the process will be the same part every time it's repeated. It's easy and fast!