views
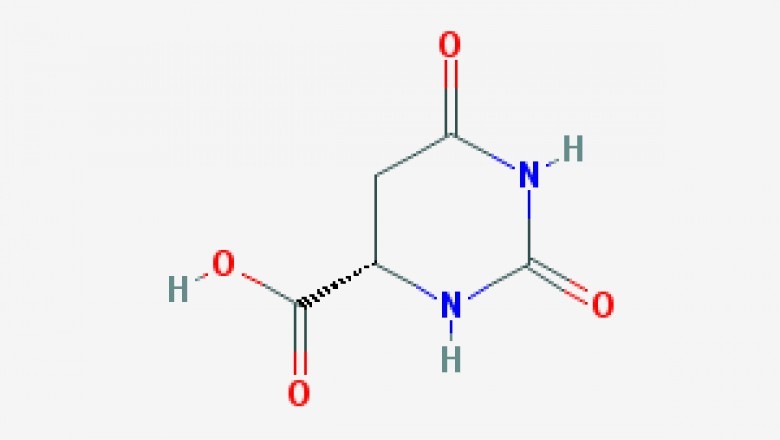
chemical companies supply chain difference
Strong industry trends - including growing international competition, industry consolidation and rising customer expectations - continue to put pressure on chemical manufacturers to improve efficiency and efficiency, especially in the end-to-end supply chain. Because these trends put pressure on industry revenue and profit margin, excellent supply chain can have a huge impact on the performance of chemical companies.
Chemical companies have invested a lot of resources to improve their supply chain, but many companies still need to make further efforts to establish a good end-to-end process, including best practice customer service.
Using our extensive collaboration with leading chemical companies, we have developed a concise framework to help other companies move forward. The framework consists of 20 elements in five categories: strategy, network, organization, process and digital implementation. Focusing on any one element cannot create excellence. On the contrary, the company must conduct a comprehensive evaluation of the supply chain, determine which elements can best meet their needs, and work within these elements to achieve performance and customer service objectives.
With the globalization of the chemical industry, competition - especially from Asia and the Middle East - is intensifying, and the cost of raw materials is becoming more volatile, thus increasing price pressure. At the same time, customers demand better service from their chemical suppliers, which is undoubtedly encouraged by the service improvements they have experienced in dealing with other industries. In addition, the industry is rapidly integrating, as evidenced by the upcoming mergers of industry giants Bayer and Monsanto, Dow and DuPont, and Clariant and Huntsman. Chemical companies in the management of products are moving towards a more subdivided direction, whether ordinary products or innovative special products.
These industry changes are putting increasing pressure on chemical manufacturers, especially their supply chains. For example, when they face greater pressure to reduce prices, they have to find new ways to make their supply chains more cost-effective. As new competition and difficulty in meeting customers affect sales, chemical manufacturers must improve their customer service performance to differentiate them from their peers, especially low-cost competitors. With the merger of major enterprises, other companies must deal with the greater market power of the merged enterprises by differentiating service performance, reducing working capital and improving asset productivity.
BCG found that excellent supply chain and strong customer orientation are the real performance differentiation factors, which create great value for industry leaders. Although chemical producers have invested a lot of time and resources in supply chain planning in the past, many enterprises still have a lot of room for improvement due to the industry's legacy infrastructure and growing market and product complexity. In addition, many companies do not pay enough attention to in-depth understanding of customer views. Therefore, chemical companies often have high logistics and inventory costs, and poor performance in supply chain indicators, which directly affect customer experience, such as delivery time and delivery service. In contrast, the leaders of today's excellent supply chain have lower cost, higher growth level, higher efficiency and higher customer satisfaction than their peers.
As an example, we find that the industry leader in supply chain performance has 14 inventory turnover times a year, while the industry leader with the lowest performance level has only 6 inventory turnover times a year. Transportation costs are equivalent to 2.2% of revenue for the best performing companies and 3.6% for the worst performing companies.
Although some of these differences reflect different business models, regions or product priorities, the differences in the way chemical companies operate the supply chain are the main determinants. By introducing lean production process, improving forecasting and planning, and integrating regional business, the company has significantly reduced supply chain costs. Achieving unimpeded alignment between planning and manufacturing enables companies to increase their asset productivity. Making a better inventory strategy will help enterprises reduce working capital and release a lot of cash.