views
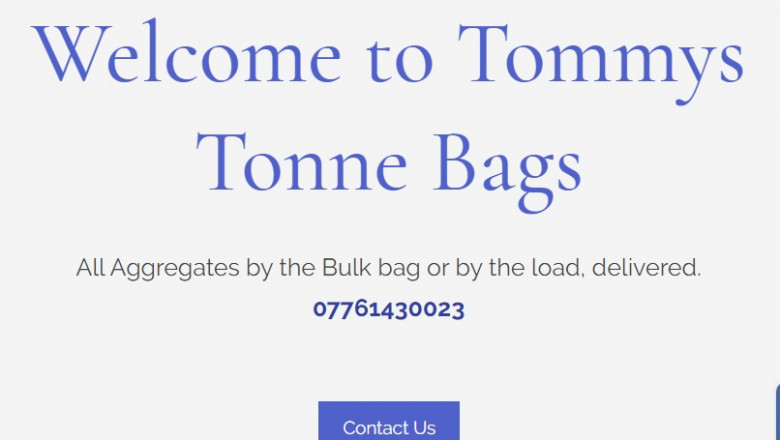
Bulk bags are a well-liked packaging solution for significant quantities of product which include aggregates and waste. They've a lot of names which incorporate, Tonne bags, Dumpy bags, FIBC's, Builders bags. Get additional information about Aggregate Bulk Bags
The array of sizes and specifications of Bulk bags are vast and each and every kind will suit a different use. The specifications also can be very detailed and technical which can at times make it difficult to determine what kind is going to be required for the essential use.
When deciding around the proper type of FIBC, the following points really should be considered;
- Physical properties or chemical properties of your intended product to go inside the bulk bag, such as:
• Required volume
• Weight of product to be contained
• Bulk density
• Contents flow characteristics
• Degree of aeration
• Particle shape and size
• Fill temperature
• Regardless of whether food grade is required
- The filling, handling, transporting, storing and emptying techniques from the FIBC.
See below for a full rundown of terms for this preferred packaging solution and their meaning. This will help to produce informed decisions concerning the form of bag required.
Terminology Info
Class of IBC = Single trip, standard duty reusable or heavy duty reusable.
Secure operating load (SWL) = this can be the capacity of your bag and relates towards the maximum weight or volume of product that the bulk bag can hold safely. It'll commonly be shown in kilograms and ranges from 250kg - 2000kg
Size = This can normally be shown in external dimensions and in centimetres.
Safety factor = Common tonne bags will have a safety element of 5:1, meaning a 1000kg capacity bag is assured to not break, rip or tear having a weight of significantly less than 5000kg. A safety element of 6:1, is actually a bulk bag made out of thicker woven polypropylene body fabric and tested to a larger standard and is generally a heavy duty or multi trip FIBC.
Filling and discharging characteristics
Plain base - This is a Standard flat base on the bottom with the bulk bag which tends to make it cuboid in shape. All common builders bags will include a plain base.
Lifting loops - Powerful loops sewn into every single corner of the bag which enables it to become picked up and manoeuvred by a fork lift truck. All FIBCs will include 4 lifting loops.
Filling inlet - You can find two types of filling inlets. They are;
Filling spout - A extended tube which permits the contents to flow in to the bag easily
Skirt major - Additional fabric in the prime in the bag which might be secured about the filling device to prevent any loss of contents, guaranteeing that each of the contents flow conveniently in to the IBC.
Baffles = Additional internal baffles are sewn onto the corners from the bulk bag. This can help to stabilise the bag and make it much more rigid and are particularly used for unstable or fluid products.
Discharge spout = A tube produced out of woven polypropylene fabric is sewn onto the bottom on the bulk bag. This offers an a lot easier flow of the contents out the bag when held more than a hopper and also the contents discharged.
Food grade = Food grade manufacturing relates towards the circumstances in which the FIBC has been manufactured and stored in ahead of delivery to client. These situations are based on strict standards which let the bag to be suitable for use for foodstuffs. Food grade bulk bags generally come with an internal polythene lamination.
You will discover two principal sorts of food grade situations;
Clean room = The manufacturing/storage facilities are free of loose threads, dirt and dust. Generally more suited to bird seed and animal feed
BRC compliant food grade bulk bags = manufactured and stored in stringent conditions that meet the BRC standards. This guarantees the food grade fibc is suitable to package food ingredients devoid of the risk of being contaminated.
Liners - An internal polythene liner supplies added protection for the contents inside. Liner can either be:
• Inserted loosely or tabbed
• Cuffed, exactly where the liner is inserted and the leading section roll over the top of the bag to create it far more safe.
• Tabbed, liner is stitched in place at the corners to ensure stability inside the bag.