views
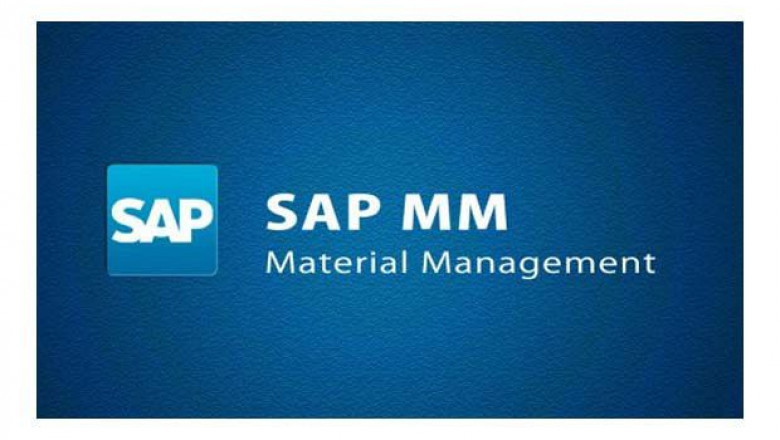
The SAP MM (Materials Management) module, which is part of the logistics domain and is frequently integrated into production and manufacturing facilities that use SAP, is one of the numerous modules available. The SAP MM module manages the procurement and inventory activities of large-scale purchasing companies, offering them direct control over inventory management, batch management, purchasing, client classification, valuation, invoice verification, and the procurement process, to mention a few. In a word, the opportunities for a career as a SAP MM consultant are practically limitless.
Materials Planning as a Concept
The user must completely comprehend the inventory technique that will be employed in the module before proceeding through the steps of the process flow. The two types of materials planning techniques in the module are Materials Requirements Planning (MRP) and Consumption-Based Planning (CBP). While the former is directed by a procurement proposal only when the anticipated inventory is triggered by a shortfall, the latter is based on forecasting and takes into account historical usage and how it may effect future demand. Both components of inventory control are largely determined by the business model chosen, and they are an integral part of the MM Process Flow, which will be detailed in the next paragraph.
In SAP MM, the Process Flow Phases are divided into the following categories.
The module's process flow considers the whole cycle that material of service must go through from the time it enters the system until it is delivered to the intended party and the transaction is completed. The MM process flow is divided into seven steps, which are as follows:
1. Determination of Requirements: As previously said, materials planning can take the form of MRP or CBP, both of which aid in establishing a clearer perspective on the requirement to acquire material.
2. Source Determination: Knowing where the company wants to source its items for production or service delivery is critical to ensuring that operations run smoothly. There may be existing long-term purchase agreements with suppliers, or alternative considerations on the procurement of materials from a different company to ensure lower overheads and higher quality may be feasible based on economic trends. Whatever method is used, this information must be recorded into the system so that quote requests (RFQs) may be issued and the organization can make an educated decision based on its requirements.
3. Vendor Selection and Quotation Comparison: The MM module's Vendor Selection and Quotation Comparison function put the user in charge of selecting and rejecting quotations based on specified criteria and demands. The user may also simulate price situations, allowing them to determine the optimum rates based on customized input data.
4. Purchase Order Processing: After choosing the best estimates, the following step is to create a purchase order (Po). The module was created to produce purchase orders automatically utilizing information from requisitions and quotations, and to transmit them to suppliers in real-time. It is also possible to generate the order manually with complete autonomy.
5. Purchase Order Follow-up: Purchase orders made to suppliers may be tracked automatically using the user-defined reminder dates. This allows the organization to have a better understanding of what is going on with the purchase orders it has given to suppliers. Checking quotes and purchasing requisitions is also available.
6. Receiving and Inventory Management: When a supplier delivers products in accordance with a purchase order, the organization is one step closer to completing the transaction. These products may be tracked using the system's specified criteria, and their receipt confirmed using the purchase order number.
7. Invoice Verification: To minimize discrepancies in quantities and amounts spent, goods sought by a purchase order should match the invoice created. Before the transaction is finalized, this information on invoices is validated in the system and provided to the allocated staff for verification.